How can your pipes, supports, and valves withstand the harshest and most corrosive conditions on Earth? The answer is protective coatings.
Integrated Protective Coatings (IPC) is an industry leader in protective coatings, from epoxy to thermally inter-diffused coatings and beyond. Our coatings provide our customers with numerous benefits including extending the life of your equipment, preventing service disruption and increasing your revenue overall.
Today, we will explain the specific benefits of each of our protective coating products, including what each coating does and which coatings are best for your project and industry. We will also cross-compare three of our most popular protective coatings in detail: Epoxy vs Electroless Nickel vs Fluoropolymer.
Protective Coating: Fusion Bonded Epoxy
IPC Fusion Bonded Epoxy creates an extremely tough protective layer that provides resistance to harsh environments like seawater, wastewater, harsh chemicals, corrosive soil, and hydrocarbons. It is initially used as a powder coating but eventually turns into a liquid when applied to pre-heated parts and is then cured.
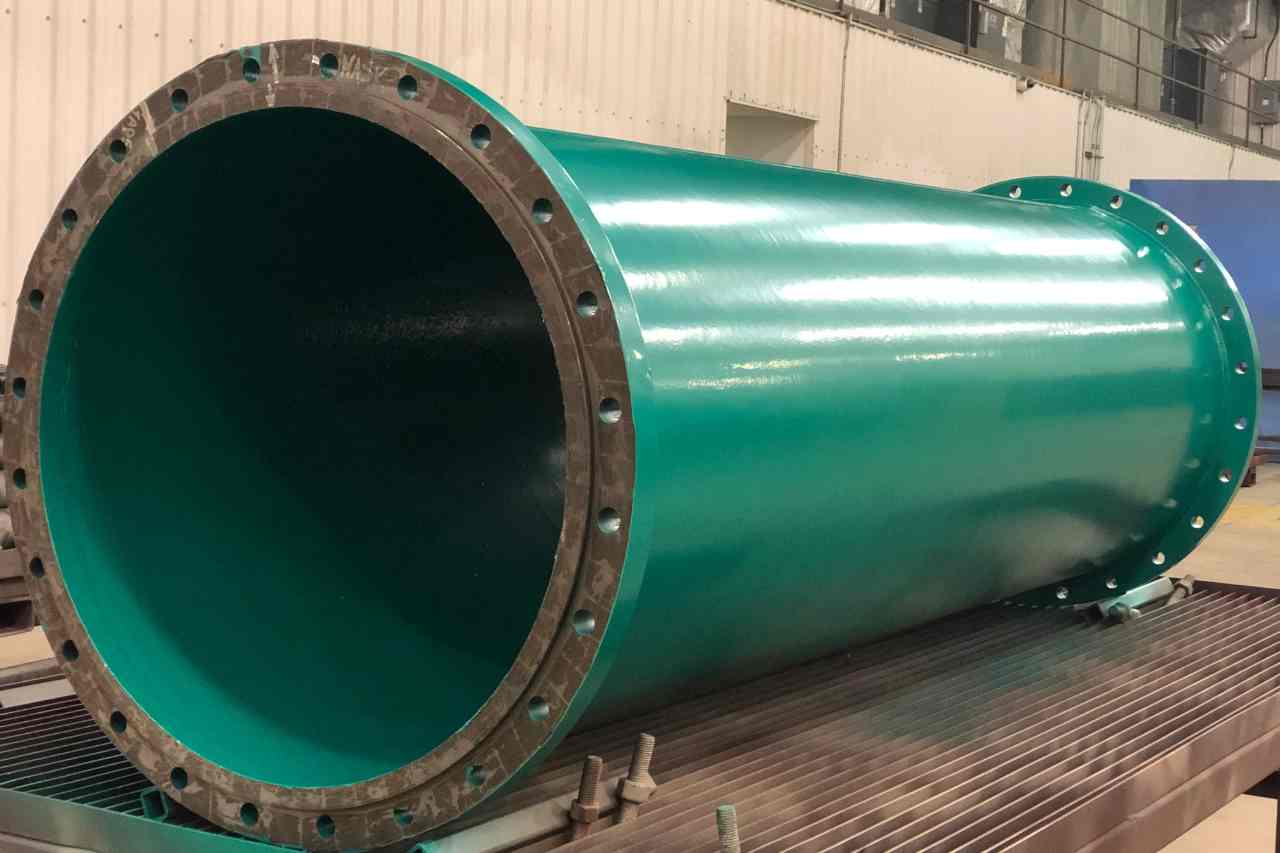
Epoxy can be especially useful for coating the inside of pumps, pipes, or other materials where a smooth, corrosion-resistant coating is required.
Features of Fusion Bonded Epoxy Coating
- Long-term performance history in municipal water & sewage, and other Oil & Gas environments
- It can be used for elevated temperature service in the presence of H₂S, CO₂, CH₄, crude oil, and brine
- Tested and certified to NSF/ANSI Standard 61, Drinking Water System Components
- Meets the requirements of AWWA Standard C213 and C550
Typical Applications
- Pipes
- Fittings
- Valves
- Couplers
- Pumps
- Extension Springs
Main Industries
- Chemical Processing
- Municipal Water & Utilities
- Oil & Gas
- Potable Water
Protective Coating: Electroless Nickel
Electroless Nickel Coating (ENC) extends the life of the substrate metal by creating a barrier to protect it from abrasion, erosion and corrosion. This process consists of nickel being evenly deposited on the metal’s surface without using an electric current.
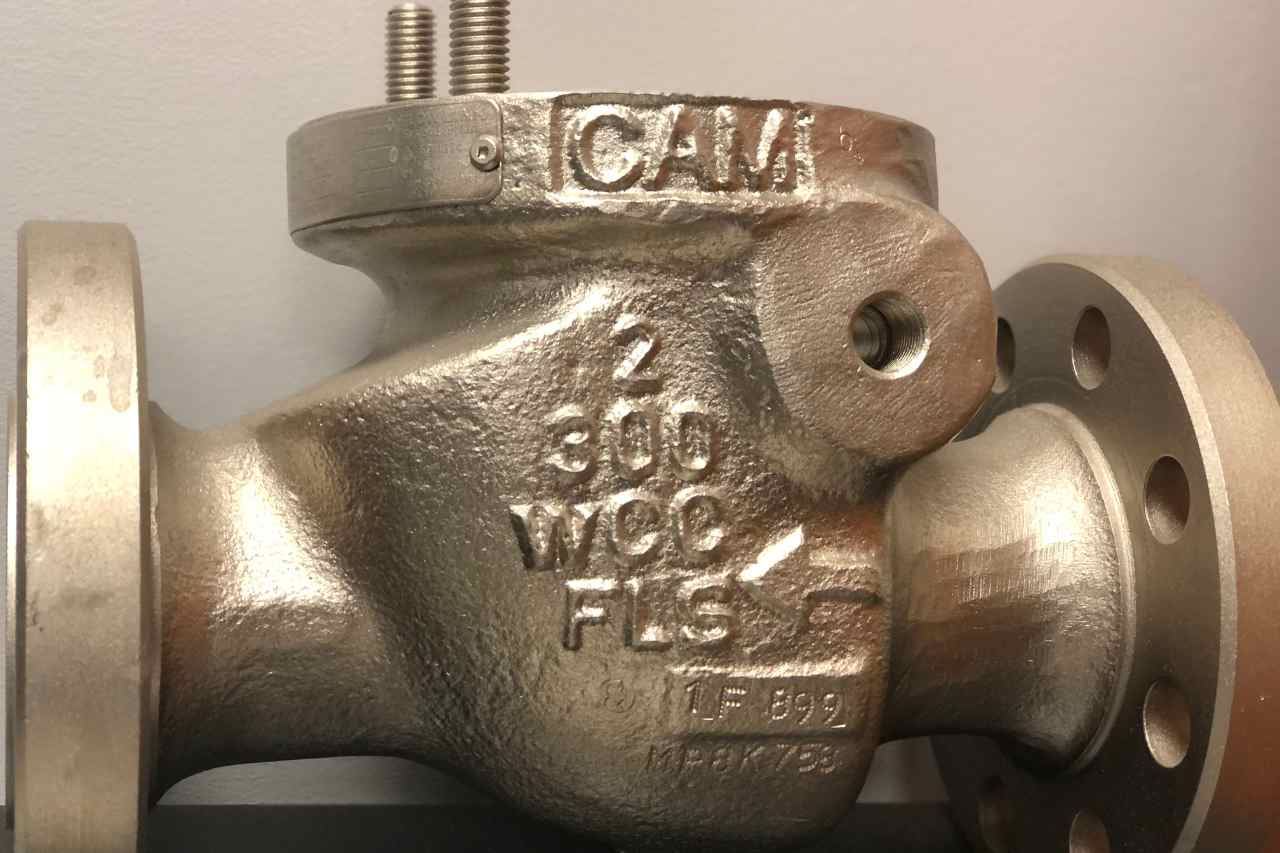
Electroless Nickel Coating is a cost-effective solution that prevents chemicals and fluids from entering the micro-cracks of the base metal and causing corrosion.
Features of Electroless Nickel Coating
- Amorphous
- Zero Porosity
- Excellent Adhesion (450 MPa)
- Microhardness (550-600HV)
- Excellent Corrosion Resistance
- Exceptional Uniformity
Typical Applications
- Valves
- Fittings
- Couplings
- Collars
- Piping Spools
- Tank
- Vessel / Process Equipment
- Packer Components
- Slide Plates
- Downhole Equipment
- Pumps & Compressors
- Rods
- Casings
- Tubulars
Main Industries
- Food & Drug
- Manufacturing
- Mining
- Municipal Water & Utilities
- Oil & Gas
Protective Coating: Fluoropolymer
IPC Fluoropolymer is an engineered high-performance blend of polymers with a host of valuable benefits. Fluoropolymer coatings allow moving parts not to stick, and make it easier to clean. These blends consist of high-performance resins and fluoropolymer lubricants.
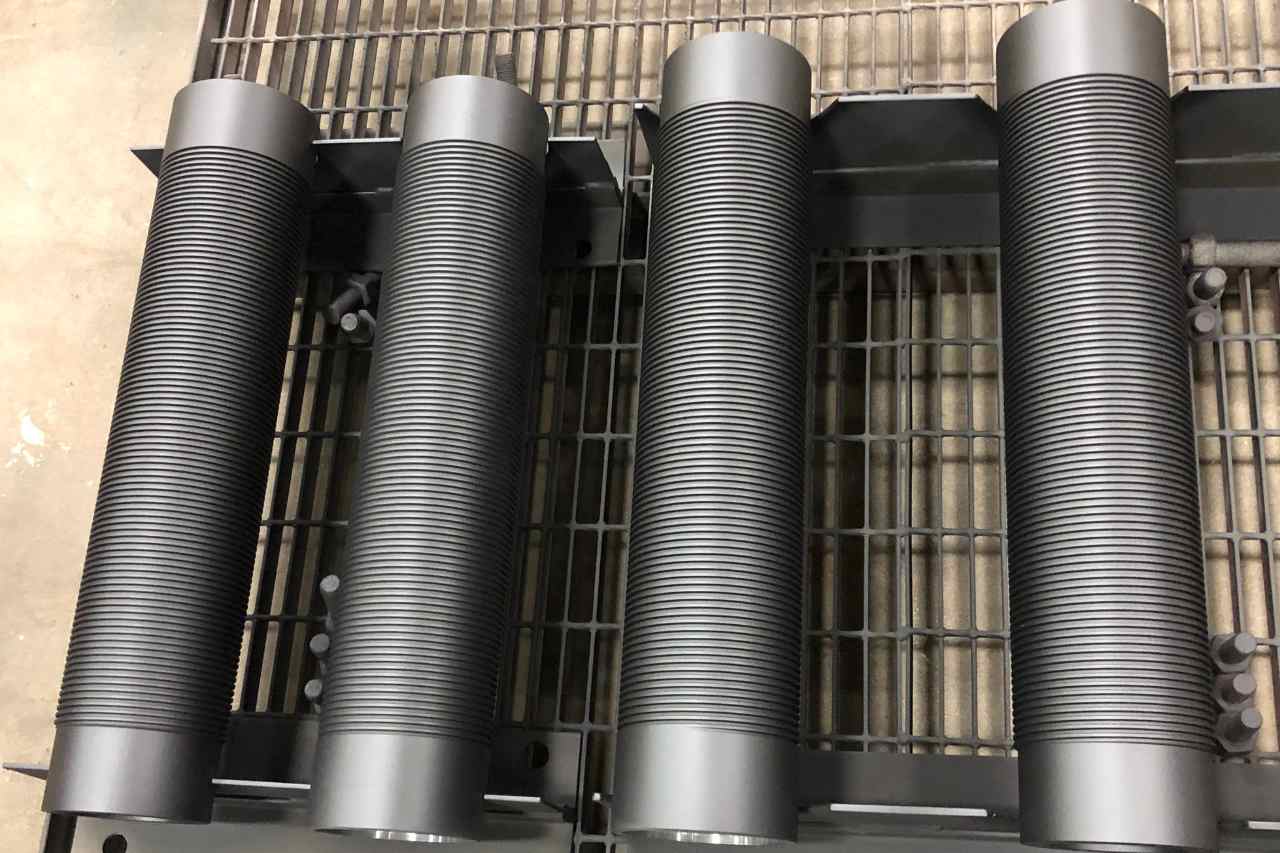
So, what does ‘polymer’ mean? According to the Britannica dictionary: “A polymer is any of a class of natural or synthetic substances composed of very large molecules, called macromolecules, which are multiples of simpler chemical units called monomers.”
Features of Fluoropolymer Coatings
- Heat, Chemical and Abrasion Resistant
- Nonstick and Low Friction
- Non-Wetting
- Electrical Hi/Lo Temp Resistance
- FDA Conforming
- It can reduce the manufacturing costs of pistons, plungers, and splines by eliminating polishing and lapping
- It can replace plating on hydraulic pistons and extend their lives in corrosive environments
- They can last longer than hard chrome plating in certain high-wear applications
- Cuts equipment maintenance costs
- Increases uptime and throughput, and safeguards product purity
Typical Applications
- Valves
- Downhole Completion Tools
- Adapters
- Food Processing Equipment
- Fasteners
- Blowout Preventer (BOP)
- Pistons
- Plungers
- Pumps
- Tanks and more
Main Industries
- Chemical Processing
- Energy
- Food Processing
- Industrial Machinery & Equipment
- Oil & Gas
Epoxy vs Electroless Nickel vs Fluoropolymer: Which Protective Coating Do I Need?
The three protective coatings we have examined here today have different purposes and are designed for different applications. Our team is here to help you and your team determine the best protective coating for your needs.
Why Should I Choose Fusion Bonded Epoxy Coatings?
The IPC System 8 (Fusion Bonded Epoxy Coating) is a perfect choice for potable water environments. It offers a low coefficient of friction and resists many gases, fluids, and chemicals. It has an NSF/ANSI 61 rating for Drinking Water System Components, making it safe for water systems. This coating protects your substrate metals in some of the harshest environments known to man, providing resistance to wastewater, hydrocarbons, harsh chemicals, seawater, and corrosive soil.
Why Should I Choose Electroless Nickel Coatings (ENC)?
The IPC Series 3000 (ENC) is our top recommendation for protection against severe corrosion attacks, including CO2, H2S, Oxygen, Chlorides and high-temperature combinations. It’s a cost-effective alternative to exotic alloys and will protect your equipment from erosion, abrasion, and corrosion. (While keeping your project on time and budget!)
This coating also has an NSF-61 food-grade rating, allowing you to protect your equipment in the Food and Drug manufacturing industries.
Why Should I Choose Fluoropolymer Coatings?
The IPC high-performance fluoropolymer coatings allow for nearly unlimited applications and are excellent for corrosion and chemical resistance in harsh environments. Along with FDA compliance and reduced friction, this coating is beneficial for many industries. Available in a full range of power and liquid forms, this coating type can be used on carbon steel, aluminum, stainless steel, steel alloys, magnesium and more. We offer a variety of fluoropolymer coatings depending on your project and needs.

Also Read: A Basic Guide on Fluoropolymer Coatings
Epoxy vs Electroless Nickel vs Fluoropolymer
Regardless of which protective coating your industry requires, IPC has you covered.
Our high-performance coating processes are backed by the rigorous quality assurance systems that we have become known for across North America.
Do you need protective coatings for your next project? Contact one of our IPC Representatives to learn more about how we can assist you. Browse our protective coating products here.