For 45 years, Integrated Protective Coatings has developed an unparalleled level of expertise in the technical side of industrial coatings and their many applications, including Xylan Coating.
With state-of-the-art equipment and a drive for quality, we provide the best coatings for the right jobs in a wide variety of industries. We know how critical it is to have the right coating and lubrication for your equipment.
We like to use our blog as an opportunity to educate those who might be new or inexperienced when it comes to industrial machinery coating and lubrication. It’s also a great place for those simply curious to know more.
By looking into different aspects of machine and equipment coating in more detail, we aim to empower you with education. So that you can be ready to make the right choice for your job, industry or project.
This post looks at Xylan coating and discusses what it is, what we use it for, the Xylan coating process and how it might benefit your company.
What is Xylan Made Of?
If you were able to look at Xylan under a very powerful microscope, you would see they are made of very long chains. These chains are completely entangled and sort of resemble a plate of spaghetti.
Every one of these very long chains is built by repeating a small molecule again and again. That is the reason why they are called POLYMERS. The word comes from greek, ‘poli’ meaning many and ‘meros’ part.
Xylan is an industrial dry film lubricant consisting primarily of one or more fluoropolymers including polytetrafluoroethylene (PTFE), perfluoroalkoxy alkane (PFA) and fluorinated ethylene propylene (FEP).
The most typical lubricant used in Xylan is PTFE for multiple reasons. First, it has the lowest coefficient of friction of any fluoropolymer. Secondly, PTFE operates effectively at low and high temperatures. Finally, PTFE is impervious to most chemicals.
Molydisulfide and graphite are the lubricants prevalent in other Xylan variations, each providing unique performance characteristics that are geared toward specific applications. The various combinations of binders and lubricants used in each resin system have allowed Whitford to produce more than 3,000 Xylan formulations.
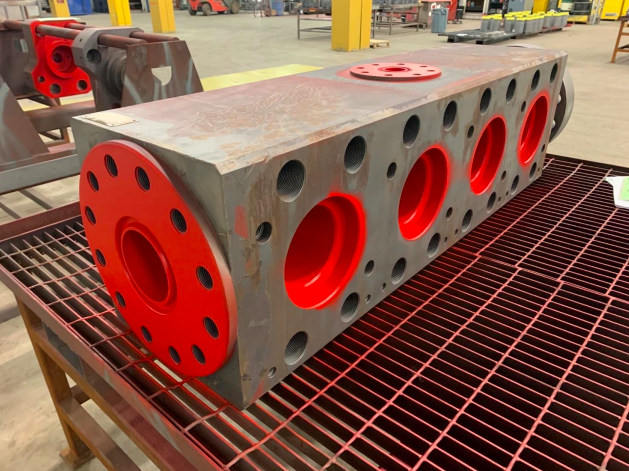
What is Xylan Used For?
Xylan has been used for many decades in a wide variety of applications. It is one of the most versatile materials to make coatings out of and it offers plenty of benefits for companies worldwide. In fact, there are eight different kinds of xylan coatings.
This enables you to not only enjoy all the benefits of using xylan as your coating material but also customize its use precisely by choosing the best formulation of the coating.
Also Read: Electroless Nickel Coating For Oil & Gas Industries
Five Benefits of Using Xylan Coatings Over Other Coatings
#1 Xylan Coatings Are Thin
They may seem like a bad thing, but the purpose of xylan coatings is to create a very thin film over other surfaces. The reason for this is that sometimes the ideal material for making a specific product might not have the right surface properties.
Xylan coatings provide the answer to this problem by simply laying a thin film over the top, thus providing just enough of the right surface material to get the job done while still enjoying all the benefits of using the best possible material for the item itself.
#2 Xylan Coatings Have High Adhesion
Many other types of PTFE coatings just won’t stick to some surfaces. Xylan coatings will. Their adhesive properties are almost unparalleled in the engineering industry.
#3 Friction is Controlled With Xylan Coatings
In the world of low-friction coatings, Xylan is a superstar. Xylan coatings provide plenty of lubrication and help to control friction in a way other coatings can’t.
#4 Xylan Coatings Are Resistant To Corrosion, Heat and Wear
This type of coating is made to resist corrosive environments, high temperatures and lots of wear. It’s the perfect combination for any engineering use.
#5 You Can Choose Between Eight Customizable Options
The versatility of this type of coating means that you can find precisely the right type of material needed for your task. Many coatings made from this material are perfect for screws or other types of threaded fasteners. Others are made specifically for automotive uses. Some types are solvent-borne, while others are waterborne. The number of applications for this type of coating is endless.
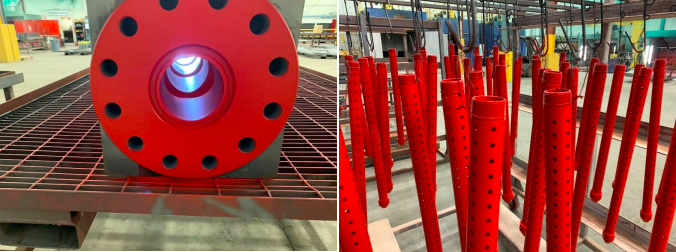
How Long Does Xylan Coating Last?
Xylan 1424 is a fastener coating used to prevent corrosion and improve makeup torque. When applied over zinc phosphate it can withstand 1,500 hours of salt fog.
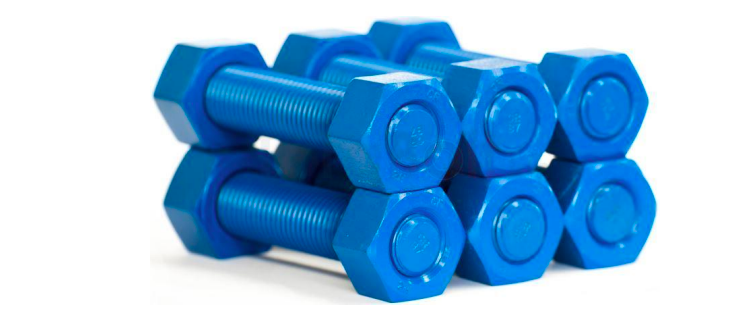
What is the Xylan Coating Process?
Xylan coatings can be applied to all types of metal substrates. Regardless of the material, the application process typically proceeds as follows:
#1 Removing any contaminants on the surface that can interfere with the formation of a quality coating layer
#2 Abrading the surface using grit blasting or sanding methods to prepare it for the coating application stage
#3 Masking any areas of the surface where coating material should not be applied
#4 Applying the coating to the surface via a conventional spray, electrostatic powder, or dip-spin method
#5 Thermally curing the applied coating to form a smooth and strong layer
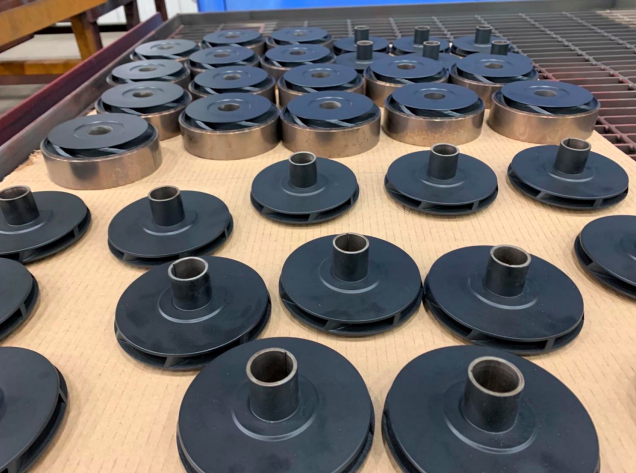
Examples of Xylan Coating Applications
Some everyday examples include:
-Medical equipment
-Oil and gas processing parts
-Electrical equipment
-Food processing parts
-Chemical processing

Integrated Protective Coatings is a Whitford Recommended Coater
We are proud to be a Whitford Recommended Coater! This status means we are recognized as a custom applicator they highly recommend for applying their high-performance coatings. We have full capabilities to apply Xylan Coatings in accordance with the recommended coaters program requirements specific to tools in Oil & Gas Industry.
IPC has shown to comply with the requirements of the program. Among the requirements to become a Recommended Coater is
- Experience in applying Whitford coatings
- Attendance at the Whitford training sessions
Whitford makes the largest and most complete line of fluoropolymer coatings in the world. We are proud to be a recommended coater thanks to our outstanding reputation in the industry. If you are interested in learning more about Xylan Coatings or any of our coating products, contact one of our in-house engineers today or give us a call toll-free at +1 800-856-4959.